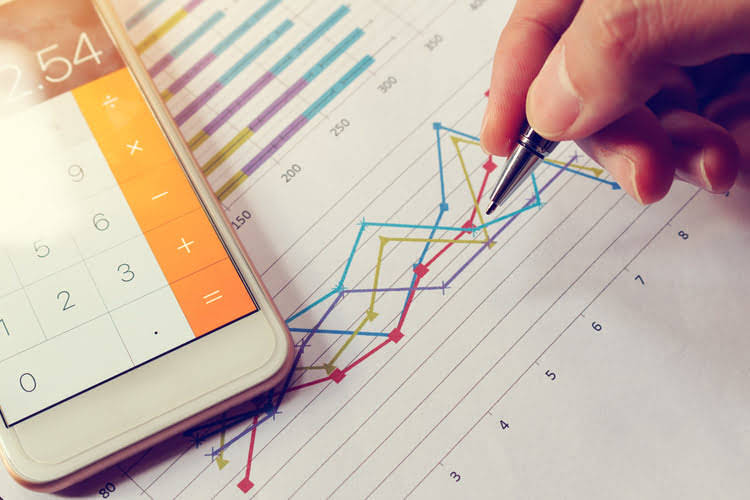
Every business unit you define must have an object and, optionally, subsidiary accounts. The object and subsidiary accounts define the kind of transaction you are working with (for example, rent, paper supplies, and so on). Some of the benefits of having manufacturing accounting a Manufacturing account include increased efficiency, improved cash flow, better budgeting, greater flexibility, and the ability to save time and money. A manufacturing account is one of the three accounts in the accounting system, the other two being a trading account and balance sheets. This information can help companies budget for future production runs and make informed financial decisions. Each of these accounts represents a different step in the production process.
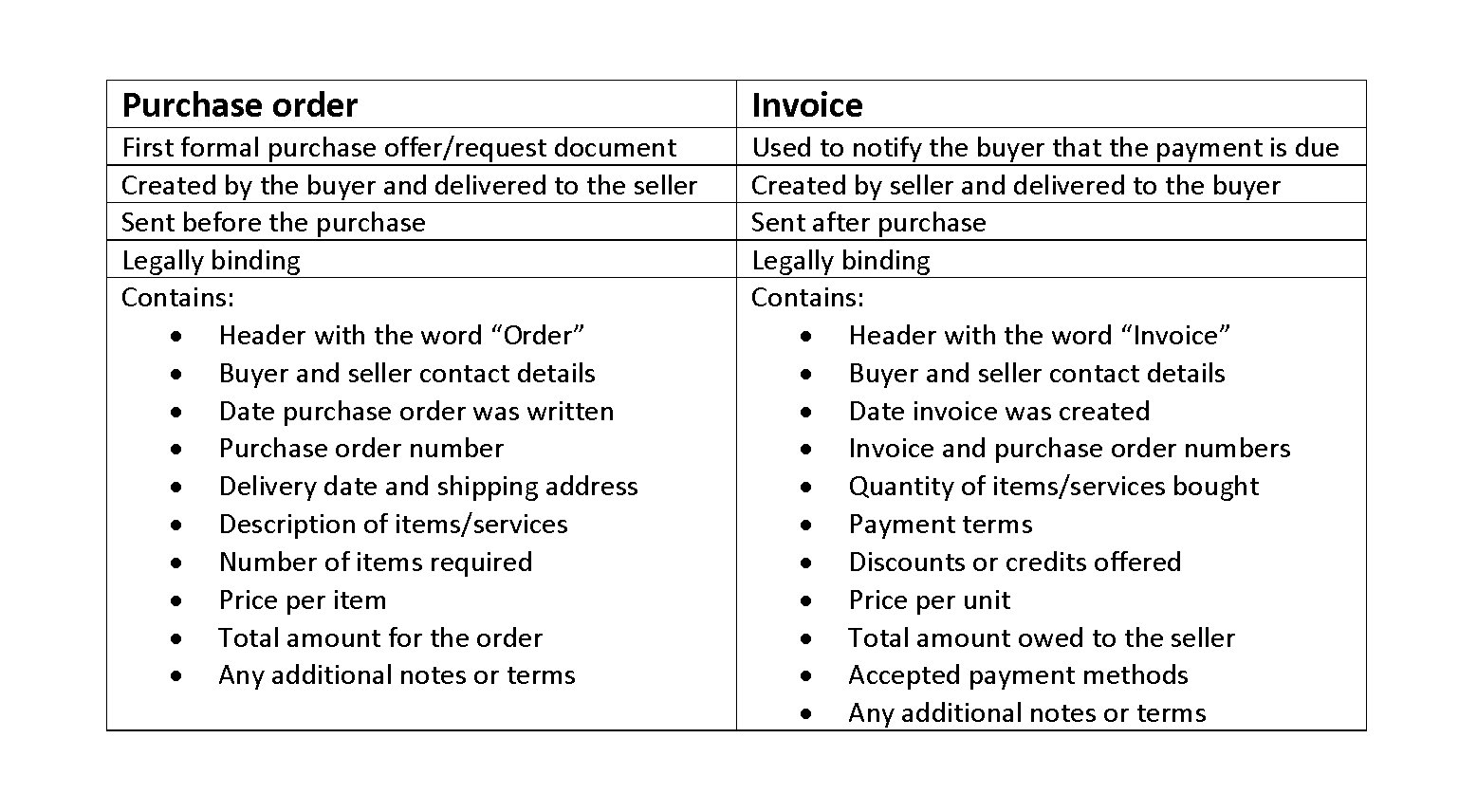
Manufacturing Overhead Costs
Subledgers are “subdivisions” of account details for categories that you do not want in the permanent chart of accounts. This information helps companies arrive at better decisions about when to buy materials and sell products. A manufacturing business is an enterprise that produces physical goods, either through machines or labor, to sell to customers. There is much to learn and many decisions to make along the way, but it is a critical task for manufacturers. Direct Labor Costs represent the wages, benefits, and insurance paid to the people who run equipment, assemble parts, and other roles that impact the production of goods.
Manufacturing Accounting: An Introductory Guide
It is therefore mostly an internal business management process aimed at better decision-making on budgeting, cost control, constraint and margin analysis, etc. An integral component of manufacturing accounting lies in efficient inventory management. Overall, accounting for manufacturing costs requires a specialized understanding of the unique aspects and complexities of the manufacturing industry.
Calculating Inventory Values
Knowing these costs is crucial for pricing products correctly and for profitability. With the help of manufacturing software, it’s easier to manage inventory, figure out the average cost of making each item according to accounting standards, and ensure there’s enough on the shelf without overflowing. This careful balancing act ensures the manufacturing business can whip up its products efficiently and cost-effectively, just like a master chef. Effective cost management lies at the core of the manufacturing sector’s financial stability and long-term profitability. By implementing sound strategies and prudent practices, you can optimize financial performance, enhance decision-making processes, and safeguard your business against potential risks.
- Production costing methods organize your cost accounting records to help management make decisions.
- Deploying a modern manufacturing planning engine can also ensure sufficient inventory is available to meet the demands of the business but that excess inventory is not causing undue strain on the business.
- For example, car manufacturers may use this approach, but a stapler manufacturer probably wouldn’t.
- Manufacturing cost accounting systems then must capture the cost of manufacturing but be flexible enough for many different manufacturing methods, processes, and technique.
- A periodic inventory system is a simplified system for calculating the value of an ending inventory.
Inventory covers the raw materials, partially completed goods, or other goods that have been manufactured but have not yet been sold. Manufacturing accounting must capture these costs, including the cost of raw materials and the cost of production. It becomes even more challenging if products are partially assembled and then inventoried or scrapped in production and sent through a rework process. The primary type of accounting used in manufacturing is known as cost accounting. It’s a form of accounting that tracks production costs in a way that managers can use to inform business decisions.
- Thus, a favorable variance may simply mean that a standard was set to be so easy to attain that all variances from it are bound to be favorable.
- Yes, manufacturing accounting software can track production costs by monitoring direct and indirect expenses.
- The job order costing method calculates costs per manufacturing project or unit, making it useful for make-to-order manufacturers, construction manufacturers, and the like.
- It provides real-time visibility into production processes and inventory, helping chemical manufacturers maintain safety standards and optimize operations.
- By employing appropriate accounting practices, businesses can accurately track costs, make informed decisions, and effectively manage their financial performance.
Material costs
This guide will help you know more about the accounting aspects of the manufacturing business. In manufacturing accounting, various financial aspects are addressed, including the cost of raw materials, labor, overhead expenses, and inventory valuation. The primary objective is to provide insights into the financial performance and profitability of manufacturing activities, enabling informed decision-making and effective cost management. Advanced manufacturing accounting software is a must-have for modern manufacturers and the manufacturing accounting teams responsible for tracking business financials. Manufacturers demand powerful, intuitive financial reporting with customizable dashboards to monitor costs, profitability, cash balance sheet flow, and financial health in real-time.
Accounting for Manufacturing Costs
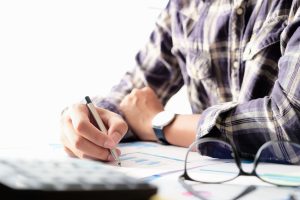
Manufacturing accounting software helps track inventory levels, costs, and movements. You can monitor raw materials, work-in-progress, and finished goods, allowing your team to make informed purchasing and production decisions. Unit of measure is critical when determining the cost of a manufactured item. For example, if a purchasing manager procures wire by the foot, an inventory clerk monitors storage by the spool, and the production manager tracks usage by the inch, problems can quickly arise. Cost accounting processes might miss the different units of measure, resulting in inaccurate reports, cost analyses, and forecasts.
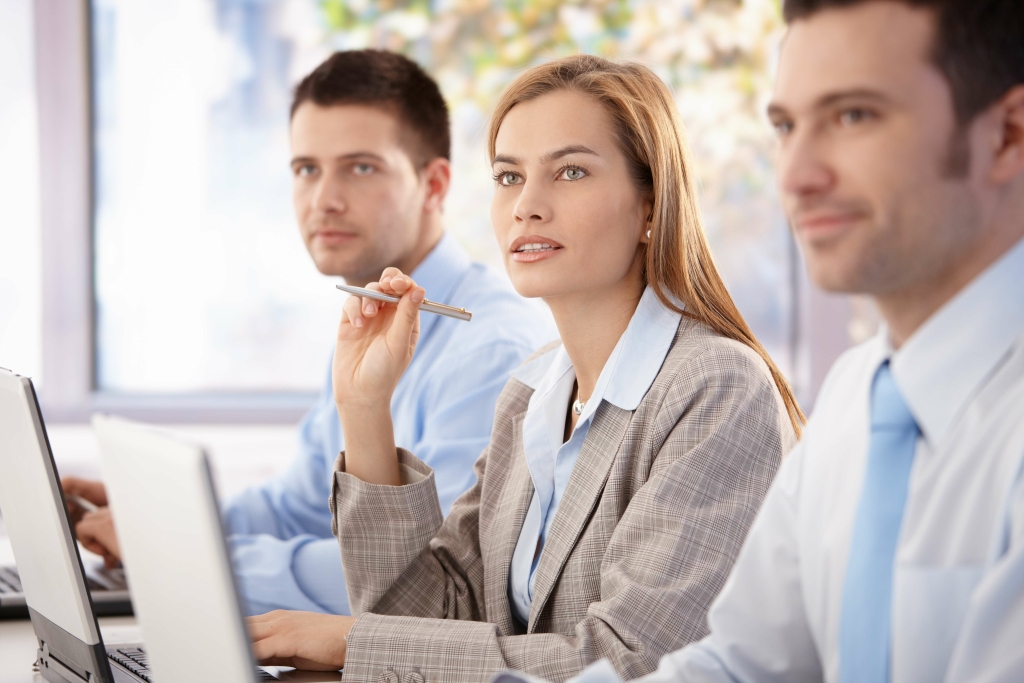
Apply for financing, track your business cashflow, and more with a single lendio account. Standard costing is very beneficial for creating and polishing budgets as it gives Grocery Store Accounting predefined cost estimates that can be measured against actual expenses. The chief disadvantage lies in having to routinely update the standards which can be arduous in case of constantly changing market conditions. Tickmark, Inc. and its affiliates do not provide legal, tax or accounting advice. The information provided on this website does not, and is not intended to, constitute legal, tax or accounting advice or recommendations. All information prepared on this site is for informational purposes only, and should not be relied on for legal, tax or accounting advice.